Rotor shears
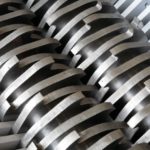
Our two-shaft rotor shears are slow running machines, which are used for pre-cutting mainly.
The material will be filled into the cutter module via a hopper. Two shafts rotating in opposed cutting directions.If a fault occurs, the cutting unit stops automatically. The cutting unit goes into reverse and then rotates again in cutting direction. After shredding the material is discharged as strips, the width of which is determined by the width of the blades. The slow running speed of the machine guarants a noise and dustless production.
Starting with our heavy series: all cutter shafts could be changed completely and the cutters could be welded!
Advantage of bomatic rotor shears:
Over dimensioned and splined cutter Shafts
In most cases the shredders of our competitors are equipped with simple and low-priced hexagonal cutter shafts. In the bomatic rotor shears we use high-grade, over dimensioned and splined cutter shafts only! A smoothly and slowly running cutting unit ensures low dust, vibration and noise generation
Fast changing of cutter shafts
The cutter shafts used in the heavy duty series could be changed completely. Therefore the bearing plates are designed in separated form and are made in two pieces. The upper part of the bearing plate could be removed, the old cutter shafts could be taken out and the new ones installed.
Protection of the blades
The current consumption of the motor is detected all the time. If foreign or hard material is detected and the current consumption is too high, the cutting unit is stopped automatically. The shredder goes into reverse direction and then returns to normal operation automatically. This will be repeated three times (amount is adjustable) normally, afterwards the shredder stops.
Rubber buffers
Our drives are fixed with rubber buffers; therefore high impact loads are absorbed and not transmitted to the gearbox. Therefore a high life time of gearbox and motor are achieved.
Welding of cutter blades
The cutter blades used in the heavy duty series could be re-worked in most cases. In our workshop the used cutters receive a hard facing by a special welding procedure.
Throughput capacities:
Baureihe | Geeignet u.a. für die Zerkleinerung von: | Durchsatz (ca., je nach Inputmaterial und Maschinentyp) |
---|---|---|
Kleine Baureihe | - Speisereste/Food Waste - Gebinde bis 2 l - Drehspäne - Speisereste/Food Waste - Knochen - Gebinde bis 30 l - Glas, Kartonagen |
50-500 kg/h 0,5 -2 m3/h |
Mittlere Baureihe | - Produktionsabfälle - Bioabfälle/Schlachthofabfälle - Gebinde bis 120 l - Papier, Glas, Kartonagen - Krankenhausabfälle |
600-1.000 kg/h 3-5 m3/h |
Schwere Baureihe | - Produktionsabfälle - Nassmüllzerkleinerung - Stahl/Kunststofffässer - PKW/LKW-Reifen - Gewerbe/Sperrmüll - Ballenware - Stahlfässer - Elektronikschrott - Zöpfe |
1.000 – 18.000 kg/h 6-80 m3/h |