Zweiwellenzerkleinerer
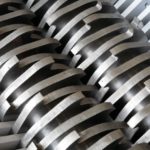
Unsere Zweiwellenzerkleinerer sind langsam laufende Rotorscheren, die überwiegend zur Vorzerkleinerung von unterschiedlichen Materialien eingesetzt werden. Je nach Art des Abfalls und der Durchsatzmenge empfehlen sich die Modelle aus unserer kleinen, mittleren oder schweren Baureihe.
Die Zweiwellenzerkleinerer von bomatic funktionieren nach folgendem Prinzip: Das Material wird über einen Trichter in das Schneidwerk eingegeben. Ein schneidendes Messerwellensystem, bestehend aus zwei Wellen mit versetzt angeordneten Messern, zieht das eingegebene Material ein und zerkleinert es streifenförmig. Die Breite der Streifen wird durch die Messerbreite bestimmt. Seitlich angebrachte Abstreifer sorgen dafür, dass das Material nach unten abgestreift und nicht wieder eingezogen wird. Der Langsamlauf unserer Zweiwellenshredder garantiert eine geräusch- und staubarme Arbeitsweise.
Vorteile der bomatic Rotorscheren:
- Überdimensionierte und evolventenverzahnte Messerwellen
Der Einsatz von einfachen und günstigen Sechskant-Messerwellen ist bei Rotorscheren weit verbreitet, hat aber viele Nachteile. Daher kommen in den bomatic Zweiwellenzerkleinerern nur hochwertige, überdimensionierte, evolventenverzahnte Messerwellen zum Einsatz. Durch die hohe Flächenpressung beim Einsatz von verzahnten Messerwellen und Messer können die Messer ohne Probleme beim Tausch von den Messerwellen wieder abgezogen werden.
- Schneller Messerwechsel
Ab einer gewissen Baureihe können an den bomatic Zweiwellenshreddern die Messerwellen komplett gewechselt werden, hierfür werden die Lagerplatten in geteilter Form ausgeführt. Zum Messerwellenwechsel werden die oberen Hälften der Lagerplatten gelöst und entfernt. Die alten Messerwellen können komplett herausgehoben und die neuen Messerwellen eingesetzt werden. Viele unserer Kunden besitzen einen zweiten Messerwellensatz. Sind die Messer verschlissen, können die Wellen vom Betreiber selbst einfach getauscht werden. Die ausgebauten Wellen können gerne zu uns zur Überholung geschickt werden (siehe Aufpanzerung der Schneidmesser).
- Störstofferkennung
Bei unseren Zweiwellenzerkleinerern wird die Stromaufnahme des Motors überwacht. Im Störstofffall, d.h. wenn die Stromaufnahme zu hoch ist, stoppt das Schneidwerk automatisch. Das Schneidwerk reversiert (dreht entgegen der Arbeitsrichtung) und dreht anschließend wieder in Arbeitsrichtung. Dieser Vorgang wird in der Regel dreimal wiederholt (dies ist beliebig einstellbar), anschließend stoppt das Schneidwerk.
- Gummipuffer
Die Getriebe unserer Rotorscheren werden in Gummipuffern gelagert. Hierdurch werden extreme Stoßbelastungen abgefangen und nicht auf das Getriebe übertragen. Die Belastungsspitzen werden durch die Gummipuffer abgefangen. Dadurch erreichen wir erheblich längere Laufzeiten an Getriebe und Motor.
- Aufpanzerung der Schneidmesser
Bei Bedarf können verschlissene Schneidmesser unserer Zweiwellenzerkleinerer bei uns wieder aufgearbeitet werden. Die Aufpanzerung ist günstiger als der Einsatz von neuen Messern, auch der Verschleiß ist bei aufgepanzerten Messern geringer. Die verschlissenen Messer werden bei uns per Roboter mit einer Hartaufpanzerung versehen und durch unsere High-Speed Fräsmaschine erhält das Messer wieder seine ursprüngliche Kontur. Durch Schleifen aller Messer und Distanzringe erhalten diese eine gleichmäßige Breite und können problemlos wieder in die vorhandene Maschine eingebaut werden.
Vorzerkleinerung von Abfällen:
Unsere Zweiwellenzerkleinerer sind für die unterschiedlichsten Abfälle geeignet und können bei Bedarf als erster Arbeitsschritt in einer Zerkleinerungsanlage vor Granulatoren eingesetzt werden. Welches Modell aus welcher Baureihe das richtige ist, hängt von der Art der Abfälle sowie der Durchsatzmenge ab. Unsere kleine Baureihe schafft je nach Material und Maschinentyp zwischen 50–500 kg Abfall pro Stunde und zerkleinert beispielsweise Speisereste, Gebinde bis 30 l, Knochen und Glas. Bei einem Durchsatz von 600–1000 kg pro Stunde sind die Modelle der mittleren Baureihe die richtige Wahl. Sie können unter anderem Produktionsabfälle, Schlachthofabfälle, Gebinde bis 120 l sowie Papier und Glas zerkleinern. Mit der schweren Baureihe werden bis zu 18 t pro Stunde verarbeitet. Aufgrund der hohen Belastung sind die Messerwellen bei diesen Maschinen komplett austauschbar und können bei Bedarf aufgepanzert werden. Die unterschiedlichen Modelle eignen sich unter anderem für die Zerkleinerung von sperrigen Abfällen wie Kunststoff- und Stahlfässern, Sperrmüll und Elektronikschrott sowie für die Reifenzerkleinerung von PKW und LKW. In der untenstehenden Tabelle finden Sie genauere Angaben zu den Baureihen von bomatic:
Baureihe | Geeignet u.a. für die Zerkleinerung von: | Durchsatz (ca., je nach Inputmaterial und Maschinentyp) |
---|---|---|
Kleine Baureihe | - Speisereste/Food Waste - Gebinde bis 2 l - Drehspäne - Speisereste/Food Waste - Knochen - Gebinde bis 30 l - Glas, Kartonagen |
50-500 kg/h 0,5 -2 m3/h |
Mittlere Baureihe | - Produktionsabfälle - Bioabfälle/Schlachthofabfälle - Gebinde bis 120 l - Papier, Glas, Kartonagen - Krankenhausabfälle |
600-1.000 kg/h 3-5 m3/h |
Schwere Baureihe | - Produktionsabfälle - Nassmüllzerkleinerung - Stahl/Kunststofffässer - PKW/LKW-Reifen - Gewerbe/Sperrmüll - Ballenware - Stahlfässer - Elektronikschrott - Zöpfe |
1.000 – 18.000 kg/h 6-80 m3/h |