


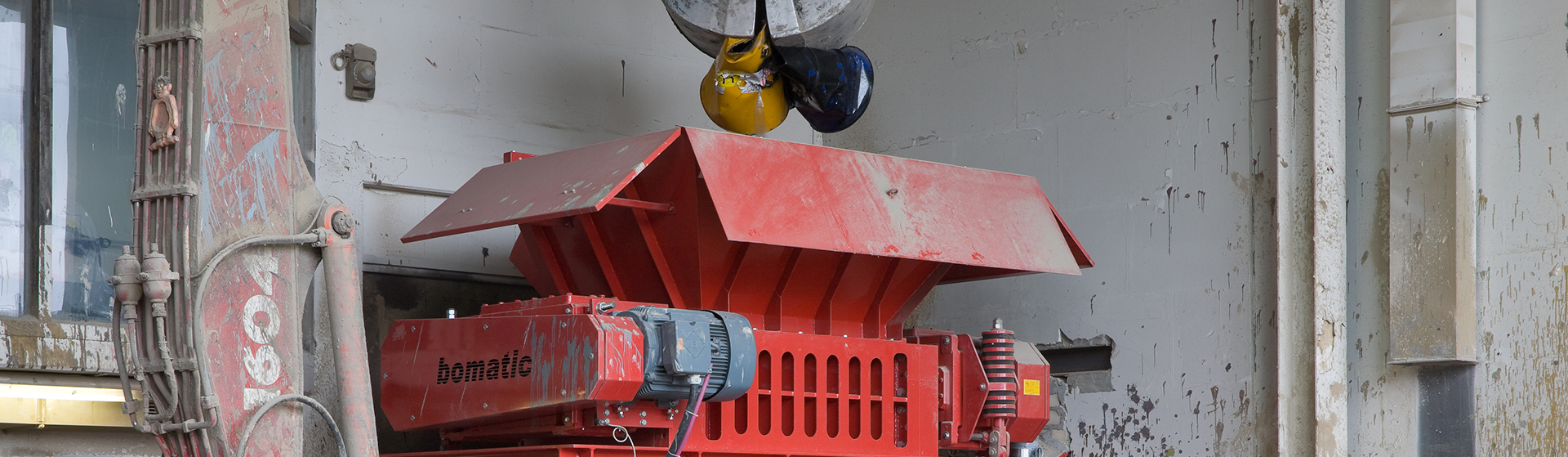








Shredding machines made in Germany from bomatic
As a manufacturer of shredding machines in the form of rotor shears, granulators, and vertical shredders, we cover various applications relating to waste grinding. Our range of service comprises the whole production process – from the design of the shredding machine to construction, in-house production, start-up, and on-site service. As producer and service provider for the waste industry we also value our environmentally friendly
production process. We offer shredding technology according to the motto "made in Germany". Our sturdy machines are known for their efficiency and maintenance-friendly operation all over the world. Regardless of whether you wish to shred paper, plastic, wood, commercial or domestic waste, we are experts with any type of material and offer the right machine for your needs.
Shredding machine with up to 220 kW: bomatic rotor shear
The bomatic rotor shear is a two-shaft shredder that is mainly used for pre-crushing. Plastic products, barrels, tyres, metals, organic waste, ship-generated wastes, food waste and much more can be crushed with ease by this shredder. More than 30 different available sizes and possible power consumption from 2.2 to 220 kW guarantee a wide variety of applications and excellent results. Our shredders are used for pre-crushing or, in other specific applications, produce the desired results in multi-stage plants. The low speed of the cutter shafts ensure low-noise and low-dust operation. In the sturdy housing, there are two counter-rotating rotor shafts that grasp the material to be crushed. Each of these shafts is equipped with splined cutting tools that interlock like scissors and crush the material in strips. To prevent material from adhering to the cutting tools, the machine is equipped with scrapers. Our rotor shears have been used in numerous businesses for many years – a clear indication of their excellent quality.
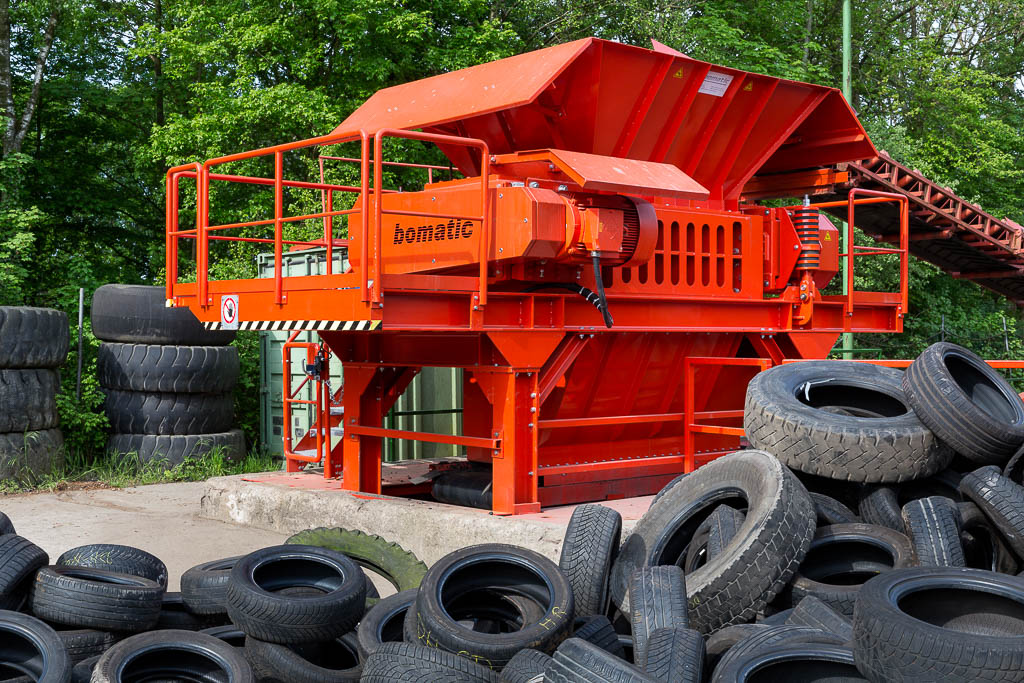
Vertical shredders & more: disintegration with Rotacrex
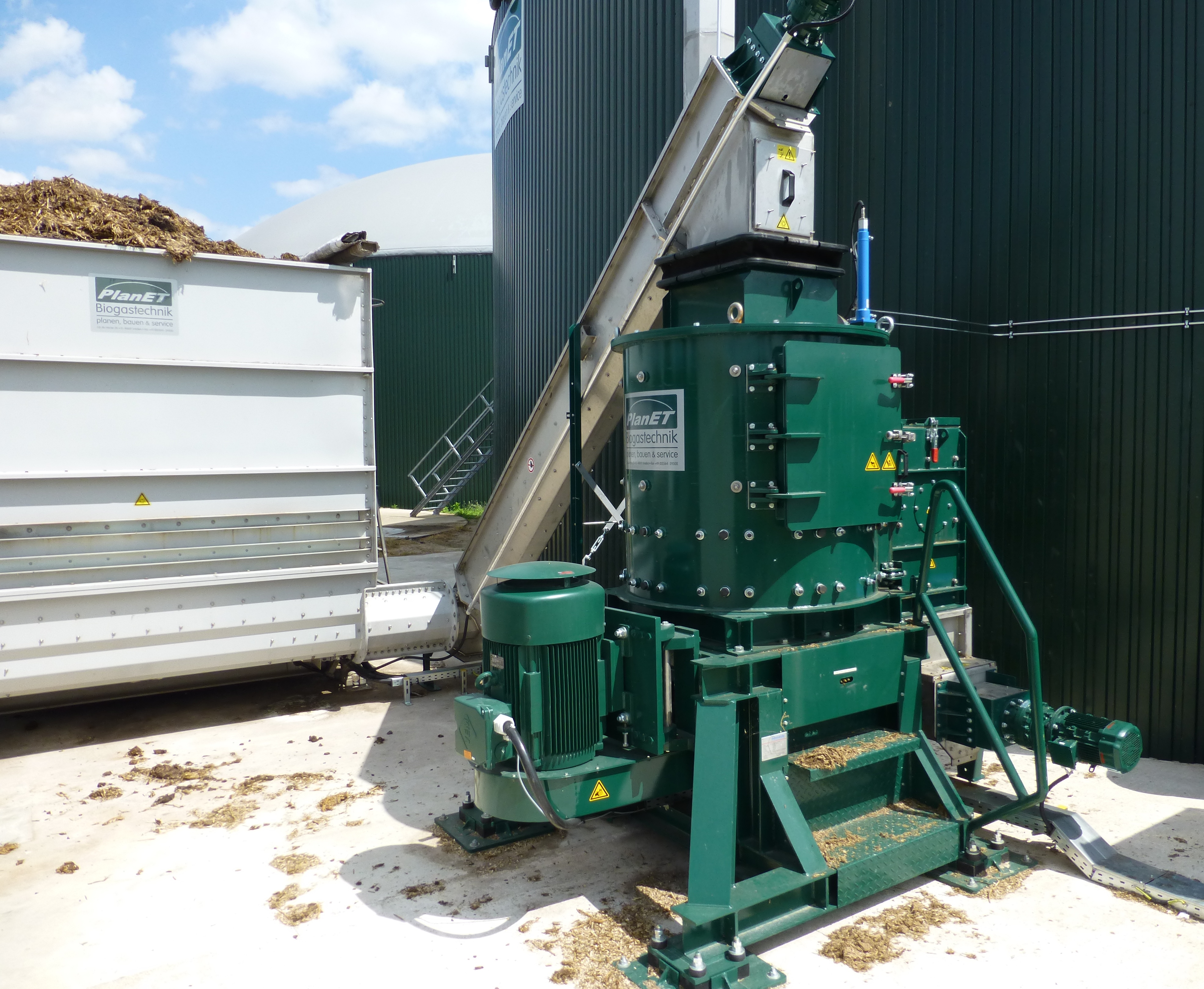
Our high-performance vertical shredders or cross-flow shredders from the Rotacrex series are ideal for disintegrating composite materials or substrates and are often used in the recycling industry or in biogas plants. A vertical striking tool rotates at high speed and crushes the material with its high impact energy. The material is fed into the system through the input opening in the middle of the housing, and it then falls onto a rapidly rotating carrier, on which what are known as "impact plates" are installed. These plates perform the main crushing work. Because of their mobile installation, the impact plates swivel away to the rear if there are any disturbing elements, which prevents damage to the machine. The desired grain size can be hydraulically adjusted using a shutter on the discharge opening. Rotacrex vertical shredders are therefore predestined for disintegrating electronic wastes – such as electric appliances or MBT waste. Moreover, an adapted version of Rotacrex shredders are used in biogas plants – to prepare the substrate of various solid materials such as manure, straw, or also in fermentation plants for organic waste treatment.
Granulators & more: Granulation with Unicrex
Granulators from the UNICREX model series are designed as fast-running, one-shaft machines and process pre-crushed materials such as tyres to produce the desired grain size. The material is crushed between rotating and stationary shears until it falls through the holes in the screen underneath the shaft. One advantage of our granulator is the quick and safe changing of the cutters. The cutter chamber can be tilted up hydraulically by 90°, which enables the best possible access to the cutters. The cutters can therefore be safely and comfortably exchanged, without having to climb into the machine.
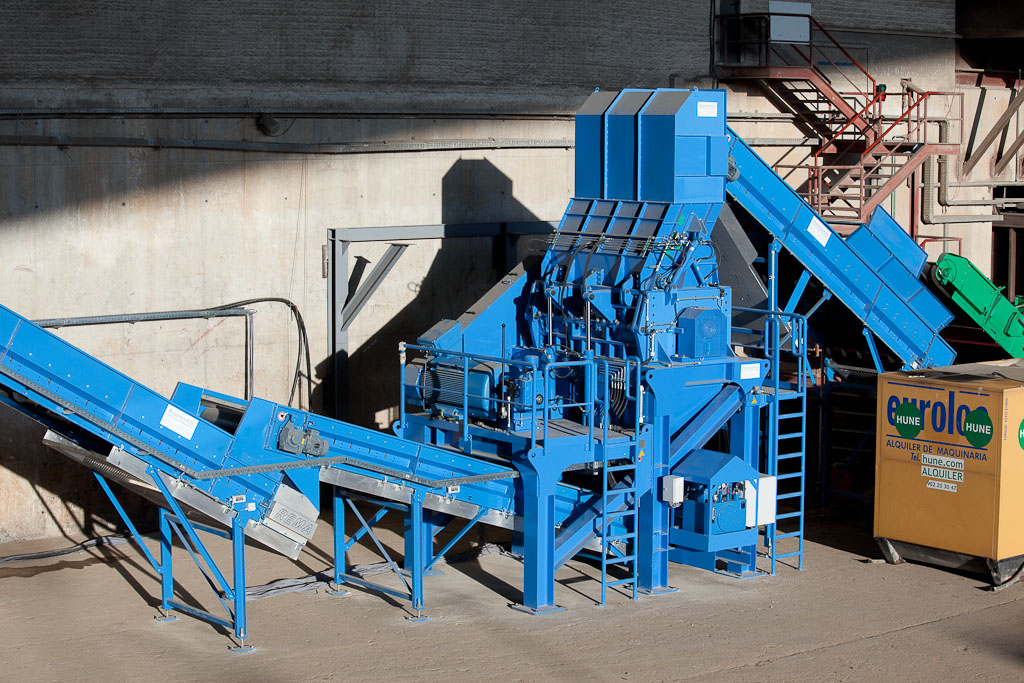
Four-shaft shredding machine & more: Producing grain sizes with bomatic B4WV/S

If a specific grain size and a slow-running machine is required, our four-shaft machine is used. Here, the material is crushed with a four-axle, cutter shaft system with offset cutters, under which a perforated screen is installed. The crushed material that is smaller than the hole size of the sieve falls through a screen basket. Particles that are larger than the screen holes are transported again by the rotor blades and are subject to another crushing step. This process is repeated until the material is small enough to exit the cutter chamber through the perforated sieve.
More than just a shredding machine
In addition to our rotor shears, vertical shredders, and granulators, we also offer customised machine design for our customers. Different cutter shapes, geometries, and also widths are no problem for us. Whether you need a feed or discharge system, post-compacting device, or hydraulically folding funnel: We have the right shredding machine for your needs! Every one of our machines is assembled, installed, and commissioned by our experienced team. Should you need a spare part one day, we are also ready to assist you with advice and, above all, the right spare part. All of the important wear parts such as cutters, scrapers, seals, and spacer rings are available in our warehouse, which saves you, as our customer, unnecessary downtimes.
Our top quality ensures durable products. Simply contact us and tell us about your project. We have the right machine for you.